Jaw Clutches & Jaw Brakes and Tooth Clutches & Brakes
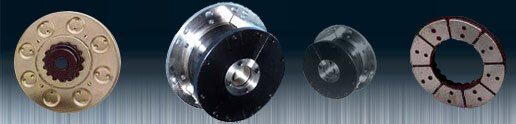
Jaw clutches and brakes – also known as tooth clutches and brakes – utilize a serrated tooth design to transfer or absorb energy from one rotating device to a second rotating device. The friction between the surfaces of the teeth of the rotating and non-rotating device allows these jaw clutches to transmit torque, and jaw brakes to hold a device in a stopped condition.
Once the torque capacity of the jaw teeth is exceeded then the jaws will disengage, dragging the teeth of one along the surface of the teeth on the second. However, this is not a recommended use for a jaw-type clutch.
Torque Handling and Variations
Jaw Clutches and Brakes / Tooth Clutches and Brakes
Jaw and tooth clutches typically transmit much higher torque in the same model size as a friction disc designs, but they are limited by engagement speed; slippage is not allowed unless the tooth form is specifically designed for it. The jaw teeth offer an easy method of obtaining a positive registration between the two devices that will be coupled together. Exceeding 100 RPM during engagement is not recommended in jaw clutches or brakes, due to violent action resulting in possible equipment damage.
Various tooth forms as well as different physical numbers of teeth are available to the designer, depending on the application. The design of the tooth form will determine the torque capacity of the clutch or the holding capacity of the brake. Using different tooth forms allows the device to slip or disengage at a predetermined point as determined by the application requirements.
Single vs. Multiple Disc Designs
Friction Clutch and Friction Brake Units
Type |
Torque Load | Cost | Tip Velocity* |
---|---|---|---|
Single Disc | Low Capacity | Lower | 775 ft/sec |
Multiple Disc | High Capacity | Higher | 200 ft/sec |
* At 5,000 RPM
Types of Friction Clutches and Brakes
Carlyle Johnson offers both single disc and multiple disc friction clutches and friction brakes. In many applications where low cost and only a small torque handling capability is required, a single friction surface will suffice. Multiple friction disc clutch and friction disc brake units offer the advantage of handling high torque loads in a compact size device.
A multiple disc clutch with seven sets of discs provides fourteen friction surfaces. The total area of these fourteen surfaces would require a very large single disc clutch or brake, to provide equal torque capability. The reason is found in elementary trigonometry. A fourteen-surface device with a diameter of 9.50" has the same area as a single surface device of 35.5"! In most high-torque applications, the space does not exist to house a single disc device of such great size.
Friction Clutch and Brake Top Velocity
Similarly, at high rotational speeds, the top velocity of a large single disc device could become a safety hazard. A 35.5" device rotating at 5,000 RPM has a velocity at its outer edge of almost 775 feet per second. How fast is that? Well, it is fast enough to be measured as a "Mach number" - in this case Mach .69. By comparison, a 9.5" multiple disc device rotating at the same speed has a velocity of about 200 feet per second.
Friction Clutch and Brake Size
A large single disc design necessitates engineering considerations and complications in bearing design, inertia loads, component size, shielding, etc. These factors can make multiple disc friction clutches and friction brakes a preferred power transmission solution where high torques are present. Single disc friction clutches and brakes tend to be larger but less costly than multiple disc friction clutches and brakes, because they contain fewer parts and are simpler to design, fabricate, and assemble.
Friction Disc Clutch and Brake Cost
Multiple disc friction clutches and friction brakes are usually much more compact although at a cost penalty due to their increased complexity. Unlike their single-disc counterparts, multiple disc friction clutches and friction brakes pack a tremendous amount of functionality into a remarkably condensed form. This allows for not only space-saving integration within diverse machinery and systems but also facilitates more efficient use of available space. For custom applications, the engineering and precision manufacturing required to produce these sophisticated components sometimes contributes to a higher production cost. Our team of dedicated engineers are happy to speak with you about your friction disc clutch and brake needs and to develop the most cost-effective solution.
Contact Our Friction Disc Clutch and Brake Experts
As a leading friction disc clutch and friction disc brake manufacturer, our experienced team can help you select the ideal solution for your application. Fill out the short contact form on this page or reach out to our service team to discuss your unique requirements.
Overview
Advantages of Friction engagement
- Soft engagement of devices to be coupled
- Engagement speed is not limited
Advantages of Single Disc Friction
Clutches & Brakes
- Best option for low-torque applications
- Cost-effective
Advantages of Multiple Disc Friction
Clutches & Brakes
- Handles high torque loads
- Safer at high rotational speeds
- Compact
CJM Friction Clutch & Brake Models
- FEA Model Fail-Safe Spring Set Electric Clutches
- FEA Model Fail-Safe Spring Set Electric Brakes
- EMA Model Multiple Disc Electric Clutches
- EMA Model Multiple Disc Electric Brakes
- HTB Model High Torque Electric Brakes
- EFS Model Spring Set Electric Brakes
- MMS & MMD Multiple Disc Mechanical Clutches
- MMS & MMD Multiple Disc Mechanical Brakes
- MOR & ORI Model Overload Release Mechanical Clutches
- MOR & ORI Model Overload Release Mechanical Brakes
- AHA Model Hydraulic / Air / Pneumatic Clutches
- AHA Model Hydraulic / Air / Pneumatic Brakes
- AFS Model Hydraulic / Air / Pneumatic Spring Set Brakes
CJM Friction Clutch & Brake Models
Downloads
Further downloads including certificates, instruction manuals and product images are available to you in our Download Center:
Downloads